微反应器内的液液非均相反应案例
(一)混合效果对于液液非均相反应的影响
Wirth团队在较早时期就利用氢氧化钠在双相溶剂体系(甲苯/水)中进行间歇釜式和微反应连续流的两相水解反应,表明了在微反应连续流动模式下增加液-液转换的界面面积对反应效果的提升有益。在上述微反应流动模式下,利用注射泵输送每股反应液在T型微混合单元中快速混合产生段塞流流型。作者分别在相同内部体积的聚四氟乙烯盘管反应器(直径0.3mm)和PMMA芯片反应器(直径0.3mm)中研究了界面面积对反应效果的影响。总的来说,在搅拌烧瓶中,反应在2min内的产率很差(<10%),而在相同的反应时间内,流动实验的结果明显更好(40-95%,取决于条件)。此外,在更高的反应温度下(50°C),使用聚四氟乙烯盘管反应器单元的段塞流方法中有更高的转化率,且可以通过降低微通道横截面来增加界面接触面积,从而进一步改善双相水解反应。

也有研究者使用四丁基溴化铵(TBAB)作为相转移催化剂,对4-叔丁基苯酚和2,3,6-三甲基苯并酚在间歇釜式和微反应连续流中的双相混合及其对反应效果的影响进行了详细的研究,如下表所示,在70°C条件下,间歇釜式微波反应器中产物苯酚74可以得到78%的收率,而在盘管反应器,芯片或填充不锈钢球的填充床微反应器中产物收率可以被进一步提高(93~94%)。由于所有的反应都是在有机溶剂(DCM)的沸点以上进行的,这就需要使用微波高压反应装置进行釜式实验,利用背压装置(5−10bar)进行微反应连续流实验。当作者使用活性更强的硫醇75为反应物时,所需的PTC量更少,反应时间更短。在相同的反应时间下,微反应连续流工艺比间歇工艺的反应效果更好。此外,微芯片反应器的转化率明显高于中尺度盘管反应器装置,这与界面面积的差异很好地吻合。此外,填充床反应器的结果最好,这也清楚地表明了混沌混合在液-液两相反应系统中的积极影响。
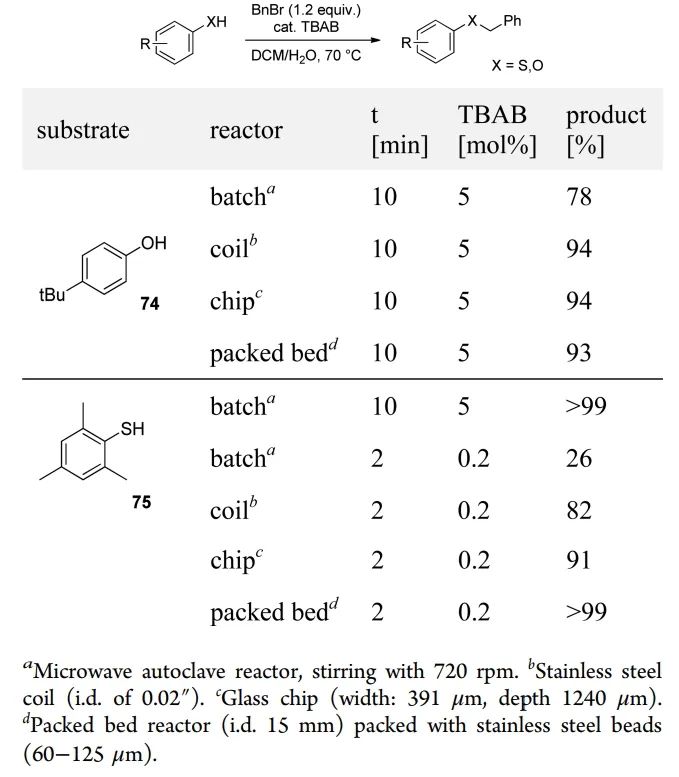
微填充床的策略被进一步应用于双相、钯催化的C−N和C−C交叉偶联反应。这些合成转化过程通常需要无机碱,而无机碱在大多数有机溶剂中是不溶的,或者会进一步产生不溶的盐,这将导致微通道的堵塞。为了溶解所有的有机和无机成分,在微反应连续流工艺中会将双相液-液混合物与相转移催化剂或两亲共溶剂结合使用。有研究者利用2-氯苯甲醚76和2-氨基苯甲酸乙酯77(如下图所示)的双相交叉偶联反应来比较盘管反应器与填充床反应器(充满不锈钢球)的混合反应效果,从反应结果来看,微填充床反应器可以在更短的反应时间内得到更好的收率。

上述研究案例清楚地表明,微反应连续流动方法中,这种双相液/液反应主要受益于界面面积和传质相关效应。然而只有在相对较快的反应中才能观察到显著的效果,而其他反应则需要额外的混合策略,例如使用填充惰性物质的填充床反应器进行持续混合强化。事实上,针对缓慢的双相反应,如伯醇与盐酸溶液的氯去羟基化反应,即使在高温/高压条件下,在间歇釜式和微反应连续流条件下反应效果也是相同的。但是,在间歇釜式工艺的放大过程中存在大量的工艺及设备方面的挑战,例如反应器尺寸、形状、搅拌速度等,因此相比来说,微反应连续流技术是一种有价值的替代方案。
(二)涉及到高温高压的液液非均相反应
如果必须在高于其中一种溶剂沸点的温度下进行液-液反应,来显著缩短反应时间,微反应连续流技术就成为研究实验室的一种强有力的手段。一个有说明性的案例是由环己烯79合成己二酸80(如下图所示)。在釜式工艺中,需要在90℃的反应条件下,Na2WO4与CH3(n-C8H17)3N]HSO4和H2O2结合,反应时间为8h。在微反应连续流反应器中,通过将反应温度提高到120°C,在15bar的条件下,这种工业相关的氧化得到了显著增强,在没有PTC的情况下,反应时间仅为20min。在进入加热的PFA盘管反应器之前,将纯环己烯79与过氧化氢和钨酸水溶液在T型混合器中混合以产生段塞流流型。由于形成了更多的极性中间体,反应混合物在反应器单元中几分钟后会变成均相溶液。重要的是,当氧化在密封容器(间歇微波反应器)中进行时,偶尔会观察到爆炸,因为当混合物不剧烈搅拌时,会有利于H2O2的放热分解,而不是期望的环己烯氧化。
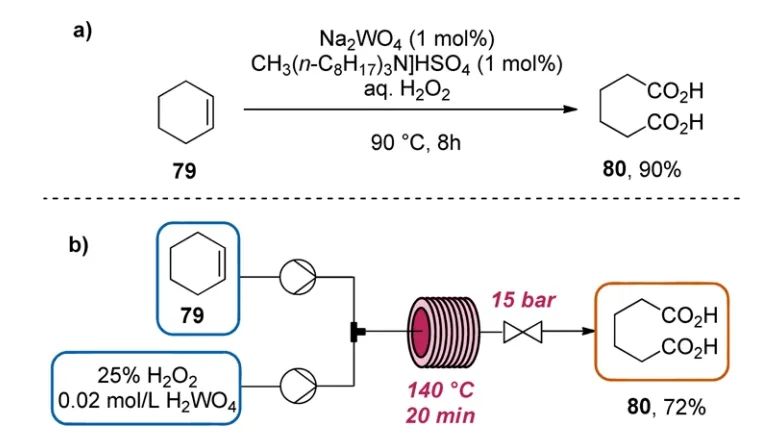
Kappe研究团队使用双相高T/p方法通过Bucherer-Bergs反应(如下图所示)合成乙内酰脲。在此多组分反应过程中,醛或酮和氰化物阴离子结合形成各自的氰醇,最终与氨和二氧化碳反应,得到所需的杂环骨架。气体原料通常通过(NH4)2CO3的热分解原位生成。在间歇釜式反应工艺中,通常将羰基化合物、KCN和(NH4)2CO3的混合物在水和乙醇中回流数小时甚至数天。而在微反应连续流方法中,EtOAc中的起始材料与试剂的水溶液混合,产生明确的段塞流流型,在哈氏合金盘管反应器中加热到120°C,压力为20bar。较高的反应压力和较低的气体顶空体积使生成的气体保持在溶液中,从而大大缩短了反应时间。

(三)液液非均相反应中在线膜分离技术的应用
双相液液反应的后处理可以使用膜分离技术进行两相的在线分离。对于单级反应,传统的分离漏斗通常更方便,因为它不需要其他的工艺优化。然而,如果形成了有毒或有害的中间体,这种分离装置可用于将生产与连续下游过程中的直接消耗结合起来。如下图所示,Jensen等人提出了一项早期的概念验证研究,该研究是由酰基氯化物和NaN3两相合成酰基叠氮化物,并随后在Curtius重排中原位消耗它们。
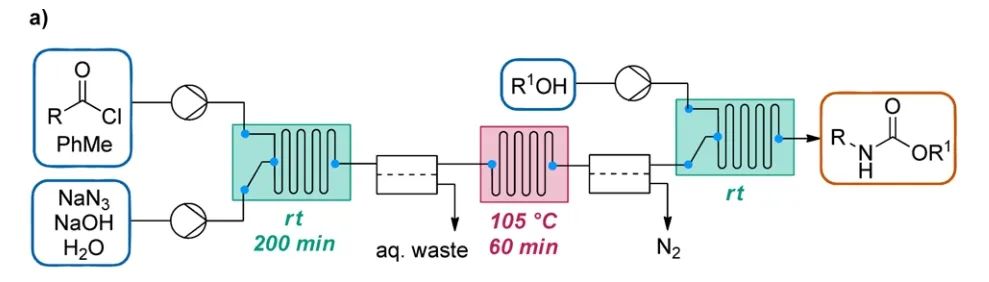
Kim团队利用相同的策略研究了重氮乙酸乙酯的制备和利用的两步;连续流合成法。如下图所示,将甲苯和甘氨酸乙酯盐酸盐81和NaNO2的水溶液混合物送入盘管反应器单元,生成所需的重氮化合物并最终提取到有机相中。两相在线分离后,危险中间体在附加的盘管反应器中与醛进行碱催化的缩合反应。

参考文献
[1]Adv.Synth.Catal.2006, 348, 1043−1048.
[2]Synlett 2013, 24, 2393−2396.
[3]Angew.Chem.,Int.Ed.2010,49, 9469−9474.
[4]Science 1998, 281, 1646−1647.
[5]Synlett 2015, 27, 83−87.
[6]Angew.Chem.,Int.Ed.2007, 46, 5704−5708.
[7]Green Chem. 2014, 16, 116−120.
关注我们,跟进微化工技术国内外最新进展
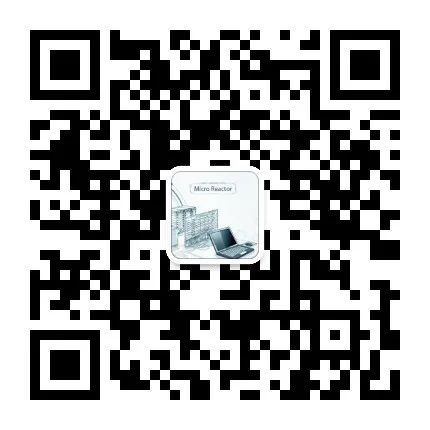