微反应器内的气液固反应
气-液-固反应通常会涉及到一些重要的化学转化过程,这些转化是通过非均相机制进行的,因此非常适合利用微反应连续流系统进行处理。氢化反应就是一个最为典型的例子,底物和氢气在金属催化剂表面吸附,氢气分子解离成原子氢并对不饱和碳-碳键进行加成,所合成的化合物最终从催化剂表面解吸。这个过程原子经济型高,选择性好,且大多数溶剂都可适用。此外,上述过程具有的高原子经济性,化学废物量少,简单的后处理(过滤催化剂和溶剂蒸发)的特点也很好地符合绿色化学原理。催化加氢反应过程中大量的非均相催化剂是可用的,该催化剂体系通常是在固体载体(碳,氧化铝,二氧化硅等)上负载贵金属(Pd, Pt, Rh和Ni)或细晶粒合金(如雷尼镍)。
上述加氢反应过程可用于饱和烯烃、炔烃或芳香体系化合物的催化加氢,还可以用于还原许多官能团,包括腈类、酰胺类、叠氮类化合物、硝基和羰基化合物等,或通过氢解去除保护基团。但是,在传统的间歇釜式反应器内氢气的利用会有着严重的安全问题,并且在环境条件下的反应有时很慢。所以对于涉及到上述反应的转化过程,目前许多都已经在微反应器系统内进行,且该技术已成为许多研究实验室的常用技术手段。
气液固反应案例
如下图所示,最简单的微反应器加氢系统主要包括五个部分:1)高压平流泵,用来输送加氢底物溶液;2)氢气瓶/高压氢气发生器,用来提供氢气;3)质量流量控制器,用来控制氢气流量;4)微填充床,用来装填负载贵金属催化剂;5)背压阀,用来控制反应体系的压力。
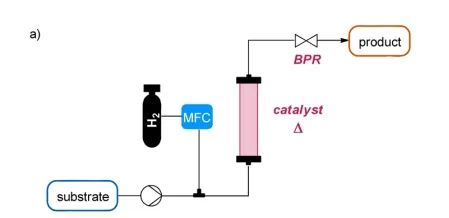
Jones研究团队开发了一种革命性的微反应连续氢化反应系统,该系统使用一个集成的电解池电解去离子水,按需生成氢气(如下图所示)。由于不需要氢气瓶,安全风险大大降低。氢气的加入由电动阀控制,并通过多孔钛模块加入到反应混合物中,以确保有效的混合效果。
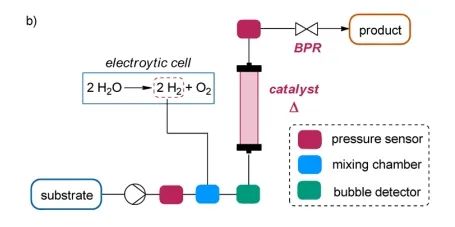
除了氢化反应外,许多研究小组利用多种非均相催化剂,包括Pt/C、氧化铝上的Ru(OH)x、MOF上负载Pd纳米粒子、 Au掺杂的超顺磁性纳米粒子和负载的氧化铁纳米粒子等,为苄基和烯丙基醇选择性连续氧化成相应的醛类和酮类提供了合适的条件。Jensen研究团队利用这一直接催化氧化策略,在缩合过程中利用Ru/Al2O3催化剂从各种苄基醇和仲胺底物合成对应的酰胺。在苄基醇初始的有氧氧化过程中,采用质量流量控制器对氧气流量进行调节。反应气体和醇溶液的混合物进入含有负载催化剂的微填充床反应器,同时将催化剂床层温度加热到80℃。停留时间为19s时,反应原料基本反应完全,且在24h实验中观察到稳定的转化率。在下游工艺中,氧气在膜分离器中被除去,然后液体流进入Silicon-Pyrex微反应器内,分别与过量的胺和尿素氢过氧化物加合物(UHP)混合反应,其中尿素氢过氧化物加合物作为氧化剂。酰胺合成需要在90-120°C条件下,22min反应时间才能完全转化。

Hermans等人开发了一种无金属催化反应方案,通过使用O2作为末端氧化剂的NOx可传播的链式氧化,将伯醇和仲醇氧化为相应的醛或酮。该反应需要催化量的HNO3作为氧穿梭剂,并结合Amberlyst-15填充床反应器进行催化反应。在100°C下,对各种底物的氧化进行迅速(4−25s),且对所需的羰基化合物具有极好的选择性。通过填料床反应器后,对反应混合物进行泄压并进行相分离。利用内嵌式的红外对气体进行实时分析,监测生成的N2O,从而获得有关自由基链传播的有价值的信息。此外,采用内嵌式全反射红外连续监测底物/产物比。与间歇式反应相比,微反应连续流工艺的反应速率明显提高,这不仅是由于催化剂的有效摩尔浓度提高,还与三元流体系中自由基链传播的延长有关。最近,同一小组引入了一种更温和的合成策略(55°C),该策略使用TEMPO固定在二氧化硅上,而不是原来的Amberlyst-15。
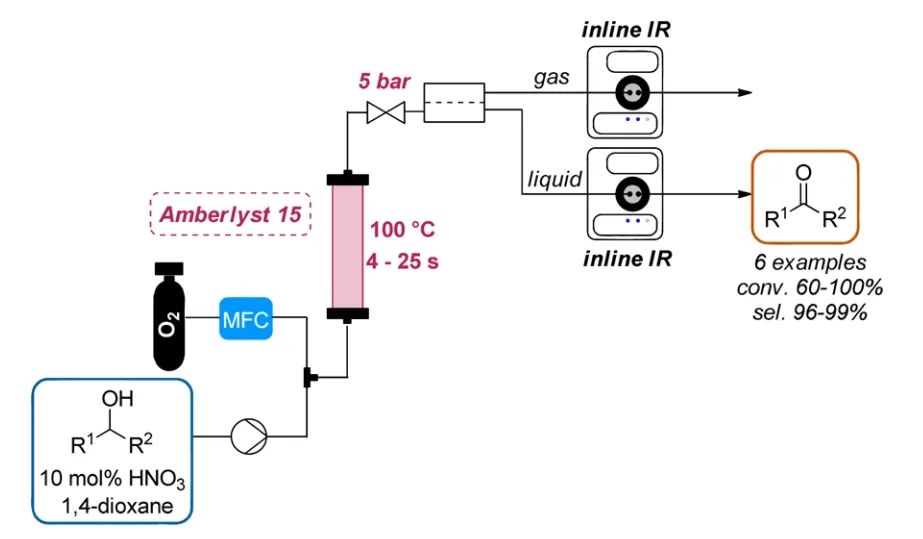
参考文献
[1]Org.ProcessRes.Dev.2014, 18, 1560−1566.
[2]J.Comb.Chem.2006,8, 110−116.
[3]Green Chem.2013,15, 1538−1541.
[4]ChemSusChem 2012, 5, 1732−1736.
[5]Green Chem. 2013, 15, 1975−1980.
关注我们,跟进微化工技术国内外最新进展
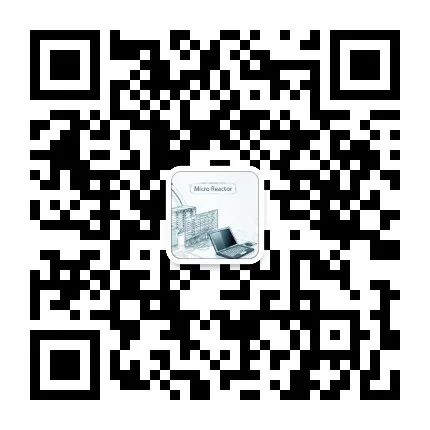